1) ISO 2859/1 sub-clause 12.6.2, states: 'If the lot or batch is of an isolated nature, it may be desirable to limit the selection of sampling plans to those, associated with a designated AQL value, that provide not less than a specified limiting quality protection. Sampling plans for this purpose can be selected by choosing a limiting quality (LQ) and a consumer's risk to be associated with it. ISO 2859-5 provides a method of establishing sequential sampling plans of discriminatory power essentially equivalent to that of corresponding plans of ISO 2859-1. In conclusion, QC practitioners tend to make their job easy and simplify the rules to follow. ANSI/ASQ Z1.9-2003 (R2018): Sampling Procedures and Tables for Inspection by Variables for Percent Nonconforming is an acceptance sampling system to be used on a continuing stream of lots for Acceptance Quality Limit (AQL) specified. It provides tightened, normal, and reduced plans to be used on measurements which are normally distributed. The ISO 2859-1 system 3.1 Description of ISO 2859-1 28 3.2 Preparing a specification for use in conjunction with ISO 2859-1 28 3.3 Classification of nonconformities and nonconforming items 29 3.4 Lots 30 3.5 Meaning of inspection level 33 3.6 Setting an inspection level 34 3.7 Preferred AQLs 36 3.8 Non-preferred AQLs 37 3.9 Setting.
The Acceptance Quality Limit (AQL) is a proven statistical instrument at the disposal for quality control when it comes to evaluating product quality.
For the purposes of this part of ISO 2859, the definitions given in ISO 2859-1 and ISO 2859-3 Licensed Copy: Institute Of Technology Tallaght, Institute of Technology, Wed Jun 28 12:50:35 BST 2006, Uncontrolled Copy, (c) BSI apply.
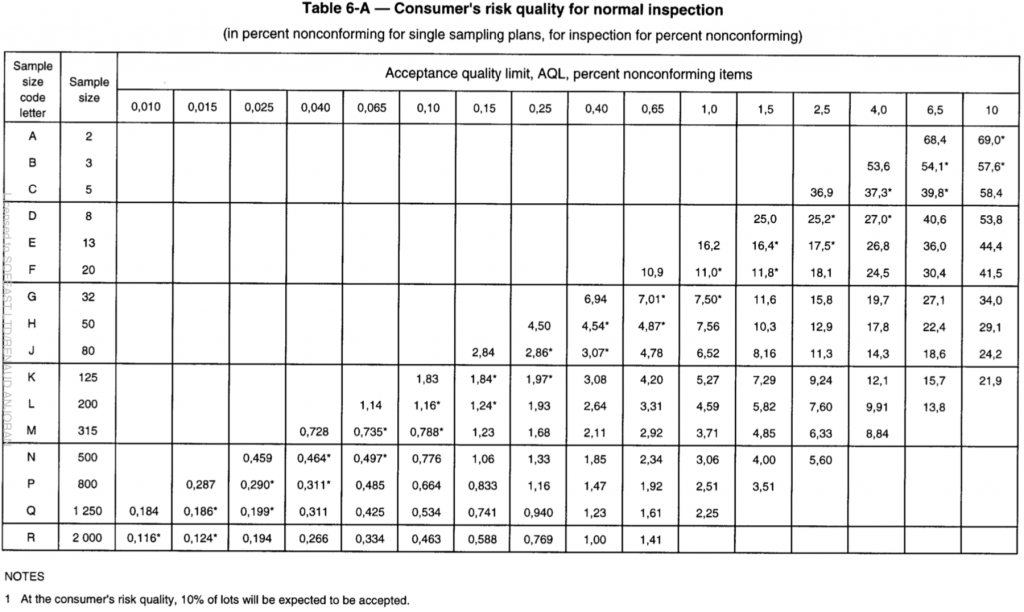
The need for quality control
In virtually every production batch, there will be defective products - however they could be extremely rare. There will always be defective products even after the QC has checked and repaired each individual product. Flawless products only exist in a perfect world, the goal is to create products that are within acceptable tolerances. Although the quality assurance systems of manufacturers of primary packaging materials are becoming increasingly more efficient through the use of innovative technologies, such as electronics and laser refraction modules, there will always be room for improvement and there are always ways to make it even better; each production run is another opportunity to create new quality standards. Notwithstanding the fact that a buyer always want a zero defect product, the supplier cannot be expected to deliver absolute zero defect goods. However, the buyer wants to control the consistent quality of purchased goods, since it does not want (too many) defects.
AQL background
Not each and every individual product can be fully checked as to its functionality. Products would become highly expensive or even instantly obsolete, as destructive test methods would destroy the product. For this reason acceptance sampling has been developed. Acceptance sampling is a statistical quality control instrument that represents a compromise between doing no inspection and a full inspection. Acceptance sampling originated way back, even before the Second World War, when the US military had to determine which batches of ammunition to accept and which bullets to reject by a destructive test method. The US army therefore developed the Military Standard 105-D, testing a few representative bullets from the production batch so they could trust the other bullets would perform on the battle field. Ultimately this might mean the difference between life and death.
The sampling scheme by which representative samples (sample rate) are selected from a population (production batch/lot) and tested to determine whether a production batch/lot is acceptable or has to be rejected is known as an acceptance plan or sampling plan administrated??? according to DIN ISO 2859 part 1. Hence the AQL, defined as the quality level that is the lowest acceptable, is a statistical procedure for determining production batch/lot quality.
AQL standard for moulded glass
Primary packaging materials made of moulded glass for pharmaceutical and cosmetic purposes are often manufactured according to quality agreements based on the 'Defect Evaluation List for Containers Made of Moulded Glass' and to the appropriate GMP Rules of the WHO (see 'Editio Cantor' )
Acceptable defect level:
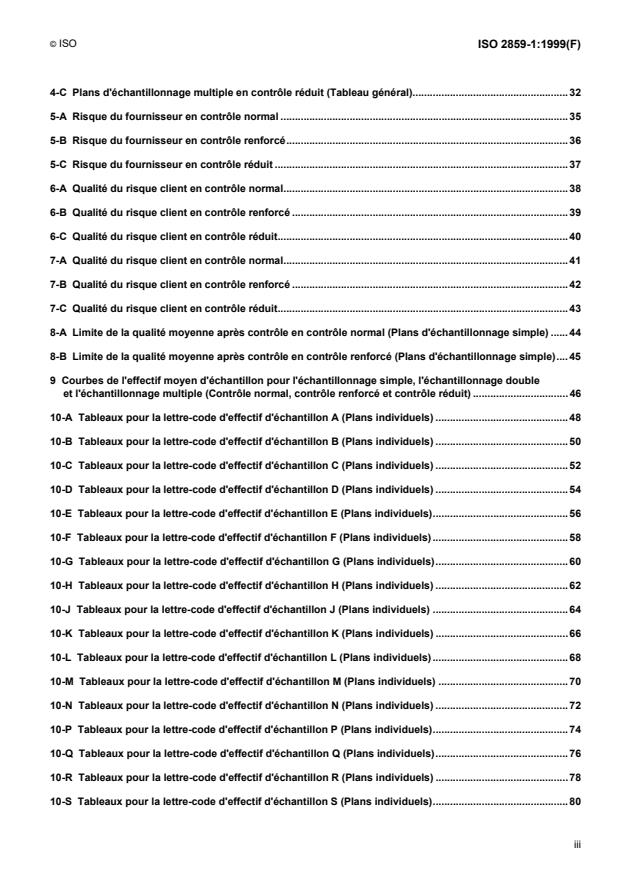
Om het maximum aantal ondeugdelijke eenheden (het acceptabele aantal ondeugdelijke producten) te bepalen, moet een kwaliteitsinspecteur weten:
- The production batch/lot size
- The inspection level
- The random sample size
- The AQL portion
To determine the correct sampling plan and acceptance/rejection level, quality inspectors rely on basically two AQL tables:
- The first table determines which 'code letter' to use based on the inspection level and production batch/lot size.
- The second table determines the sample size and maximum number of defects that can be accepted based on the code letter and AQL.

General inspection level II is the most widely acceptable level for moulded glass bottles.
Table 2 -Single sample plans for normal inspection according DIN ISO 2859-1
Classification
The most widely acceptable defect classes and AQL portions for moulded glass:
- Defect class 1, critical defect; Consequently AQL defect portion -
- Consequence: Packaging material not usable
- Defect class 2A, major defect; Consequently AQL defect portion 0.65
- Consequence: Usability of packaging material markedly impaired
- Defect class 2B, major defect; Consequently AQL defect portion 1.5
- Consequence: Usability of packaging material moderately impaired
- Defect class 3, Minor defect; Consequently AQL defect portion 6.5
- Consequence: Usability of packaging material slightly impaired
Copy Of Iso 2859 1 Free Download
Defect counting rules:
The number of defects found for each defect class is typically calculated according to the following procedure:
- Each individual defect is counted.
- If one bottle has more than one defect, it is only count once.
- In case multiple defects at one bottle belong to multiple defect classes, the lowest AQL sets the acceptable defect limit.
Example of a defect evaluation
QA have noticed an inside open glass bubble (defect# 14.05.11) in two production batches of 550,000 moulded glass bottles. According to the current defect evaluation list this represent defect class 2A, i.e. an AQL defect portion of 0.65. What would be the correct sample size and the acceptable number of defects?
Counting results for batch 1 (demo)
- The inspection level is determined to be General inspection level 'II'. Consequently, the code letter is 'Q'. (table 1)
- Consequently the random sample size from the total production batch is 1,250 units. (table 2)
- Defect class 2A, major defect; Consequently an AQL defect portion of 0.65
- Acceptance number of defective bottles is a maximum 14 at an AQL portion of 0.65 (table 2)
- The rejection number of defective bottles is 15 or more at an AQL portion of 0.65 (table 2)
Resultaten van het tellen bij partij 1 (demo)
Quality inspectors found the following numbers of defective bottles:
- 12 bottles with different defect characteristics within defect class 2A
- 10 bottles with different defect characteristics within defect class 2B
- 12 defects at defect class 2A is less than the highest acceptable number of defects (14).
- 10 defects at defect class 2B is less than the highest acceptable number of defects (21 see table 2).
Result: Production batch 1 is release/approved as none of the defect classes (2A and 2B) are met.
Counting results batch 2 (demo)
Quality inspectors found the following number of defective bottles:
- 14 bottles with different defect characteristics within defect class 2A
- 22 bottles with different defect characteristics within defect class 2B
- 14 defects at defect class 2A is equal to the highest acceptable number of defects (14).
- 222 defects at defect class 2B is above the highest acceptable number of defects (21 see table 2).
Result: Production batch 2 is rejected/not approved as one of the defect classes (2A and 2B) is not met.
The above examples, counting rules and AQL portions used are for demonstration purposes only.
Sampling procedures for inspection by attributes -- Part 1: Sampling schemes indexed by acceptance quality limit (AQL) for lot-by-lot inspection
This part of ISO 2859 specifies an acceptance sampling system for inspection by attributes. It is indexed in terms of the acceptance quality limit (AQL).
Its purpose is to induce a supplier through the economic and psychological pressure of lot non-acceptance to maintain a process average at least as good as the specified acceptance quality limit, while at the same time providing an upper limit for the risk to the consumer of accepting the occasional poor lot.
Sampling schemes designated in this part of ISO 2859 are applicable, but not limited, to inspection of
- end items,
- components and raw materials,
- operations,
- materials in process,
- supplies in storage,
- maintenance operations,
- data or records, and
- administrative procedures.
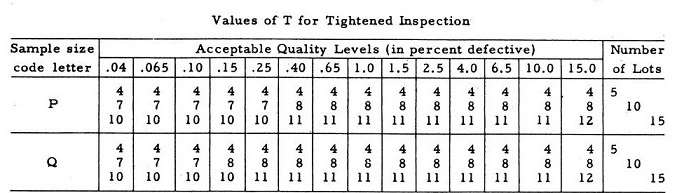
These schemes are intended primarily to be used for a continuing series of lots, that is, a series long enough to allow the switching rules (9.3) to be applied. These rules provide:
- a protection to the consumer (by means of a switch to tightened inspection or discontinuation of sampling inspection) should a deterioration in quality be detected;
- an incentive (at the discretion of the responsible authority) to reduce inspection costs (by means of a switch to reduced inspection) should consistently good quality be achieved.
Sampling plans in this part of ISO 2859 may also be used for the inspection of lots in isolation but, in this case the user is strongly advised to consult the operating characteristic curves to find a plan that will yield the desired protection (see 12.6). In that case, the user is also referred to the sampling plans indexed by limiting quality (LQ) given in ISO 2859-2.
Available for SubscriptionsAvailable in Packages- ISO 2859-Sampling Procedures for Inspection by Attributes Package
Iso 2859 1 Free
Your Alert Profile lists the documents that will be monitored. If the document is revised or amended, you will be notified by email. You may delete a document from your Alert Profile at any time. To add a document to your Profile Alert, search for the document and click “alert me”.
Copy Of Iso 2859 10
Please first verify your email before subscribing to alerts.Your Alert Profile lists the documents that will be monitored. If the document is revised or amended, you will be notified by email. You may delete a document from your Alert Profile at any time. To add a document to your Profile Alert, search for the document and click “alert me”.
Already Subscribed to this document.Your Alert Profile lists the documents that will be monitored. If the document is revised or amended, you will be notified by email. You may delete a document from your Alert Profile at any time. To add a document to your Profile Alert, search for the document and click “alert me”.
Content Provider
International Organization for Standardization [ISO]